Blog entry by rweret erwert
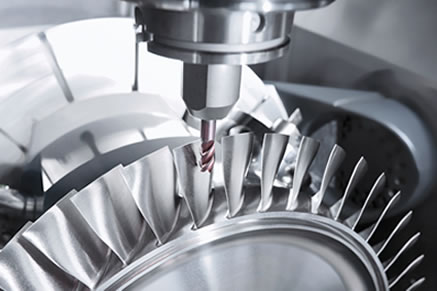
Choosing the best metal fabrication for your custom metalwork is essential. This is the most crucial step when making a very good product. There are many factors to consider when picking a metal for a fabrication project due to the many options available. In this blog post, you will learn about the different fabrication materials you can use and compare each metal to select the one that best suits your needs.
Types of Metals for Custom Fabrication
Various metals are used for custom metalwork projects. From constructing copper flashing, aluminum ladders, stainless steel tanks, or carbon steel ducting. Here’s a simple guide to different types of metal fabrication:
Carbon Steel
Steel with a carbon content is frequently utilized in industrial settings. It is robust in tough industrial settings and simple to deal with. This fabrication material is frequently utilized for tanks, ducts, access equipment, and structural steel. It’s crucial to apply high-temperature paint or galvanization to carbon steel components to stop corrosion.
Stainless Steel
The high chromium content of stainless steel inhibits rusting. Although this metal alloy choice costs more than carbon steel, corrosion resistance is necessary for applications like food processing tanks and containers.
Aluminum
Aluminum metal is a lightweight, corrosion-resistant metal useful in the automotive and aerospace sectors. Owing to its minimal maintenance needs, it is also utilized for military and industrial access equipment.
Copper
Electrical parts are frequently made from copper, which is well-known for its remarkable heat and electricity conductivity. This fabrication material flexibility makes it a top option for metal manufacturing applications. When exposed to oxygen and moisture, copper develops a protective patina similar to several other metals, preventing further corrosion and improving the metal’s appearance.
Titanium
Thanks to its reputation for strength, titanium is frequently used in harsh settings. These metal alloy choices are preferred in the aerospace, medical, and automotive industries, where lightweight and resistance to corrosion are critical. They have almost twice the strength of aluminum and are substantially lighter than steel. Because of its high melting point and inherent corrosion resistance, it is even more suitable for a wide range of applications. Even though titanium metal has many advantages, machining it can be difficult.
Factors to Consider When Choosing a Metal
Making the best decision while working on a metal selection project requires weighing several important considerations carefully. Using four main perspectives, let’s explore these issues:
Strength and Durability
An important factor to consider is a metal’s strength and durability. The load-bearing requirements of the intended use determine the required levels of strength. Steel and titanium are well-known metals with excellent tensile strength and toughness that are ideal for structural components subjected to severe loads or stress. These metals are highly desirable because they can withstand extreme pressure and maintain structural integrity.
Close up Image of a Stainless Steel Sheet a durable choice for custom fabrication
Resilience to Corrosion
When using metals in severe or outdoor environments subjected to chemicals, moisture, or airborne contaminants, corrosion resistance is crucial. Because of their ability to withstand corrosion, metal alloy choices like stainless steel, aluminum alloys, and particular specialty alloys are highly valued. Even in hostile settings, they ensure long-term durability and performance by forming protective coatings or passive oxide layers that insulate against corrosion.
Weight
One important factor to consider is the metal’s weight, especially in applications where weight reduction is a top priority. Lightweight metals like magnesium and aluminum offer substantial weight reductions than conventional steel or iron alloys. Due to this benefit, they are perfect for transportation, automotive, and aerospace industries, where losing weight increases performance, reduces overall operating costs, and improves fuel efficiency.
Cost-effectiveness
When choosing a metal, cost-effectiveness is crucial in balancing budgetary restrictions and performance objectives. Despite their superior metal properties, some metals may need more money for materials and processing. The initial expenditure must be carefully weighed against the long-term advantages and performance of the chosen metal. Choosing affordable solutions that satisfy project needs without sacrificing quality or safety is the greatest way to maximize resource usage and get the best value.
Application of Different Metals in Fabrication
Thanks to its many applications based on the unique qualities and attributes of different metals, metal fabrication is an important sector of the economy. Here are how different metals are used in fabrication projects across various industries:
Construction Sector
Architectural features and structural components are fabricated from various metals, making metal fabrication essential to the building sector. Building and bridge structural frameworks, beams, and columns are frequently steel-made because of their strength and longevity. For window frames, roofing, and façade cladding, aluminum alloys are preferred due to their corrosion resistance and lightweight nature.
Auto Industry
Manufacturing vehicle components in the automotive sector heavily relies on metal fabrication techniques. Steel’s strength and crashworthiness make it the preferred material for structural reinforcements, body panels, and chassis. In body panels, engine parts, and suspension systems, aluminum alloys are increasingly utilized to lighten vehicles and increase fuel economy.
The Aerospace Sector
The aerospace industry mostly relies on the metal fabrication process for producing solid and lightweight parts for spacecraft and airplanes. Titanium is widely utilized in vital aerospace applications like engine components, aircraft frames, and structural fittings because of its exceptional strength-to-weight ratio and resistance to corrosion. Advanced aluminum and composite materials are also used because of their performance qualities and ability to reduce weight.
Retail Stores
Metal fabrication is common in producing consumer items, including electronics and home appliances. Because of its strength, hygienic qualities, and visual appeal, stainless steel is popular for cookware, kitchen appliances, and utensils. Because of their exceptional heat conductivity and lightweight design, aluminum alloys, including computers, tablets, smartphones, and laptops, are frequently used in consumer electronics manufacturing.
Comparison of Metals for Specific Applications
When selecting metals for particular applications, several factors must be considered to ensure optimal performance and suitability. Here are three key criteria for comparison on metal selection:
Strength-to-Weight Ratio
The strength-to-weight ratio is crucial, especially in applications where weight reduction is paramount. Metals with a high strength-to-weight ratio offer superior strength relative to their weight, making them ideal for applications where minimizing weight is critical. For example, titanium exhibits an exceptional strength-to-weight ratio, making it a preferred metal alloy choice for aerospace and automotive components where lightweight yet robust materials are essential. Aluminum alloys also offer a favorable strength-to-weight ratio, making them suitable for applications requiring structural integrity without adding excessive weight.
Aluminum bars are arranged neatly illustrating their lightweight and versatile properties for fabrication
Machinability
Machinability refers to a metal’s ease of machining or shaping using various fabrication techniques. Metals with good machinability can be efficiently shaped, drilled, or milled to meet specific requirements. Stainless steel, for instance, has excellent machinability, allowing for precise fabrication of intricate components in industries such as automotive and consumer goods. On the other hand, while possessing exceptional strength properties, titanium can be challenging to machine due to its high strength and hardness, requiring specialized equipment and techniques for effective fabrication.
Weldability
Weldability is another critical factor in metal material selection, particularly in applications requiring joining or welding of components. Metals with good weldability can be readily welded without compromising structural integrity or introducing defects. Steel is renowned for its excellent weldability, making it a versatile choice for various fabrication projects across industries such as construction and automotive. Metal alloy choices like aluminum also exhibit favorable weldability, making them suitable for applications requiring lightweight structures or intricate weld joints.
Here’s a table summarizing the comparison of metals for specific applications:
Metal Strength-to-Weight Ratio Machinability Weldability Common Applications
Steel High Moderate High Construction, Automotive
Aluminum Moderate High Moderate Aerospace, Automotive, Electronics
Copper Moderate Moderate Moderate Electrical Wiring, Plumbing
Stainless Steel High Moderate High Food Processing, Medical Equipment
Titanium High Low Moderate Aerospace, Medical Implants
Custom Fabrication Techniques for Different Metals
Custom fabrication techniques are essential for shaping metals according to specific project requirements, necessitating a thorough understanding of each metal’s properties and behaviors. Below is an in-depth overview of fabrication techniques tailored to various metals:
Steel
Welding: Welding is a fundamental process in steel fabrication, allowing different steel components to be joined together. Common welding techniques include arc welding, where an electric arc melts the steel surfaces and adds filler material to create a strong bond. Methods like MIG (Metal Inert Gas) and TIG (Tungsten Inert Gas) welding offer versatility and precision in joining steel pieces.
Cutting: Steel can be cut through various methods, such as oxy-fuel cutting, which combines oxygen and fuel gas to melt and remove metal. Plasma cutting utilizes a high-velocity jet of ionized gas to cut through steel, while laser cutting and waterjet cutting provide precise and clean cuts with minimal heat-affected zones.
Forming: Forming processes like bending, rolling, and stamping shape steel into desired configurations. Press brakes are commonly used for bending operations, while roll-forming machines and stamping presses create intricate shapes and patterns in steel sheets or plates.
Aluminum
Welding: Aluminum welding requires specialized fabrication techniques due to its low melting point and high thermal conductivity. TIG welding, which uses a non-consumable tungsten electrode, is often preferred for producing clean and precise welds on aluminum. Additionally, MIG welding with a suitable aluminum wire and shielding gas is commonly employed for its efficiency and ease of use.
Cutting: Aluminum can be cut using methods similar to those used for steel, including plasma cutting, laser cutting, and waterjet cutting. These fabrication techniques ensure accurate cuts without compromising the integrity of the aluminum material.
Forming: Aluminum’s malleability allows it to easily form into various shapes through bending, stretching, and deep drawing. Hydraulic presses and roll-forming machines shape aluminum sheets and profiles according to specific design requirements.
Copper
Welding: Copper welding techniques often involve TIG or oxy-acetylene welding. These methods require precise control of heat input to prevent overheating and ensure proper fusion between copper surfaces.
Cutting: Copper can be cut using conventional methods such as shearing, sawing, or plasma cutting. Care must be taken to minimize heat buildup during cutting to avoid thermal distortion and burr formation.
Forming: Copper’s excellent flexibility makes it well-suited for forming operations like bending, rolling, and drawing. However, its tendency to work hard necessitates periodic annealing to maintain formability and prevent cracking during forming processes.
Stainless Steel
Welding: Stainless steel welding techniques include TIG welding, MIG welding, and spot welding, among others. Special consideration is given to selecting filler materials and shielding gases to maintain the corrosion resistance of stainless steel welds.
Cutting: Stainless steel can be cut using plasma, laser, and waterjet. These fabrication techniques ensure clean cuts with minimal heat distortion, preserving the integrity of the stainless steel.
Forming: Stainless steel can be formed through bending, rolling, and deep drawing. However, this metal fabrication process is high strength and has work-hardening characteristics that may require specialized tooling and equipment to achieve the desired shapes without excessive deformation or cracking.
Titanium
Welding: Titanium welding techniques include TIG welding, electron beam welding, and laser beam welding. Titanium welding processes must be conducted in an inert gas environment to prevent contamination and ensure high-quality welds.
Cutting: Titanium can be cut using methods such as abrasive cutting, waterjet cutting, and EDM. These fabrication techniques minimize heat input and prevent the risk of ignition or contamination during cutting.
Forming: Titanium can be formed through hot-forming or cold-forming processes, including bending, forging, and spinning. Special attention is given to temperature control and tooling design to prevent work hardening and maintain material flexibility during forming operations.
Best Practices for Selecting the Right Metal
Choosing the best metal for fabrication is a critical decision that can significantly impact its success. To ensure an informed choice, it’s essential to consider several factors. Here are some best practices for selecting the appropriate metal:
Collaboration With a Metal Fabrication Expert
When undertaking a project involving metal properties, consulting with a metal fabrication expert is essential. By partnering with a fabrication expert, you can leverage their expertise to select the most suitable metal based on strength, durability, corrosion resistance, and cost-effectiveness criteria. They can also offer valuable guidance on the fabrication techniques required for different metals, helping you make informed decisions from the outset of your project.
An assortment of metal alloys offering diverse options for custom fabrication projects
An assortment of metal alloys offers diverse options for custom fabrication projects
Prototype Testing
Before proceeding with large-scale production, it’s advisable to conduct prototype testing using different metal materials. Prototyping allows you to assess the performance of each metal under real-world conditions and identify any potential issues early in the development process. By testing multiple metals, you can compare mechanical properties, machinability, weldability, and overall suitability for your specific application. Prototype testing provides valuable insights that inform the final selection of the most appropriate metal for your project, minimizing risks and ensuring its success.
Environmental Considerations
Environmental factors are increasingly important in metal selection, particularly in sustainability-related industries. Some metals may have a greater environmental impact due to extraction methods, energy consumption, and recyclability. It’s essential to evaluate the environmental footprint of each metal throughout its lifecycle, from extraction to disposal or recycling. Metal alloy choices with lower environmental impact, such as recycled or sustainably sourced materials, can help reduce your project’s carbon footprint and contribute to environmental goals.
Sustainability of Different Metals
Sustainability considerations play a crucial role in metal selection, with many industries favoring renewable, recyclable, and eco-friendly materials. While metals such as titanium and copper may have higher energy requirements for extraction, they possess unique metal properties, justifying their use in specific applications. When assessing the sustainability of different metals, consider factors like resource availability, energy consumption, emissions, and end-of-life disposal options. Prioritizing sustainable materials in your metal selection process can align your project with environmental objectives and promote a more sustainable future.
Conclusion
Selecting the appropriate metal for your custom fabrication project can be minute, often requiring expert guidance. Companies specializing in sheet metal fabrication, like XTJ, offer valuable insights into metal properties and recommend the most suitable option for your metalwork project.
Consulting with such experts ensures consideration of critical factors, including metal thickness and finishing requirements. With our extensive expertise in custom fabrication, XTJ stands ready to assist you in choosing the optimal metal for your project. Contact us today to begin your custom fabrication project journey.